
T610 TURRET SLITTER
The T610 twin-turret duplex slitter rewinder produces unmatched throughput by allowing the operator to setup cores on the outer rewind mandrels during the slitter runtime. This gives the T610 turret slitter rewinder a significant advantage over standard slitters due to the reduced downtime. A differential rewind system compensates for web gauge variation, allowing the T610 to rewind non-uniform web constructions. Differential air shafts are available to accommodate a wide range of core IDs and provide a high speed rewind roll change-up. Additional features such as outer shaft supports, extend the roll weight capacity on the rewind shafts. When the rewinding is complete, the T610 turrets the rewind shafts and automatically continues winding while finished rolls are unloaded onto a roll recieveing tree. After the finished rolls have been removed, new cores are positioned during slitter operation for maximum throughput. A set-up is as simple as recalling a new file through the color touch screen. Operators never need to handle rewind tooling, handle shafts, setup knives or manually move rolls.
SPECIFICATIONS
Description | Imperial | Metric |
---|---|---|
Rewind Roll Diameter | 24" | 610 mm |
Unwinder Roll Diameter | 40/50/60/72" | 1000/1300/1500/1850 mm |
Max Web Width | 63/70/80" | 1600/1800/2050 mm |
Max Web Speed | 2000/2600 fpm+ | 600/800 mpm+ |
WATCH IT IN ACTION

Auto Roll Lock Differential Air Shafts
Deacro’s roll lock differential air shafts are ideal for tension sensitive materials, clean running environments and rapid setup applications. Roll lock segments are stacked across the shaft eliminating the need to setup spacers. When rewinding is complete, the roll locks can automatically disengage for the finished rolls to be unloaded. Deacro offers a variety of designs for custom cores and with technology that can lock and unlock automatically and lock in forward and reverse winding directions.
Closed-Loop Rewind Tension Control
The closed-loop rewind tension control option gives operators the optimum level of control over the rewinding process. This option is particularly helpful for converters running tension-sensitive materials such as light gauge, extensible films. Load cells are used to read the actual tension and adjust the torque to the rewind shafts automatically for closed-loop rewind tension control. The slitter control system automatically adjusts the air pressure in the rewind shafts. This adjusts the rewind tension to match the load cell readings. This maintains the desired tension based on the base tension setting, taper tension setting and current roll diameter.

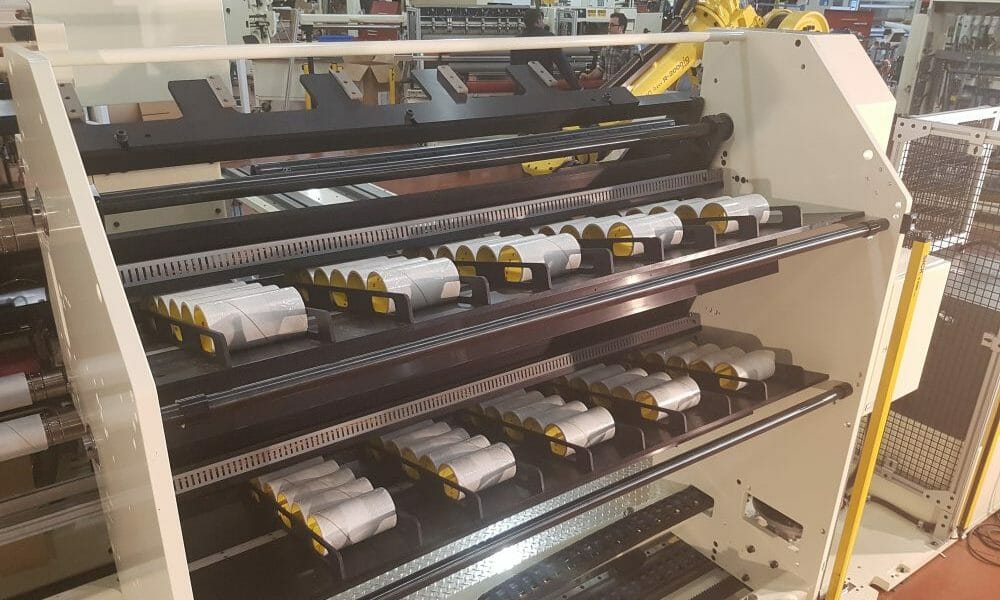
Auto Core Placement
Core can be automatically located on the rewind shafts by a variety of methods. A core hopper holds several sets of cores for fully automatic operation. Cores can be loaded as a set or individually depending on cycle time requirements.
Servo/Auto Laser Core Positioning
To reduce setup time, lasers can be supplied to indicate the rewind core locations. Operators simply line up the cores with the lasers. The servo positioning version eliminates the initial setup and positioning of the lasers. The operator waves a hand near a sensor to initiate the laser to move to the next required core position as saved in the file recipe to match the positioning of the knife locations.
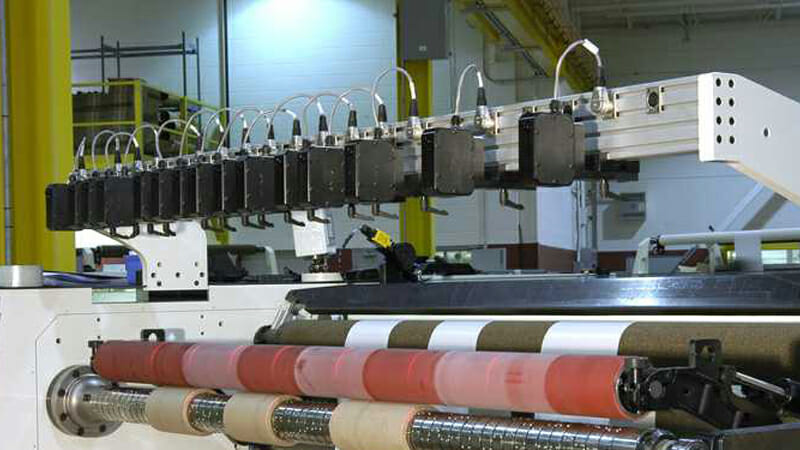
Manual Laser Core Positioner
The manual laser core positioning system uses multiple lasers to indicate the required location for cores on the rewind shafts. The position of the lasers can be easily adjusted by the operator with quick disconnects and tool-less locking. After locating the lasers, operators simply line the edge of the cores with the laser for quick and accurate positioning
Roll Pushing
Automatic unloading of finished rolls onto a receiving tree can reduce the slitter downtime between set changes and provide increased safety for operators. The electric design provides smooth removal of the finished rolls at the touch of a button.
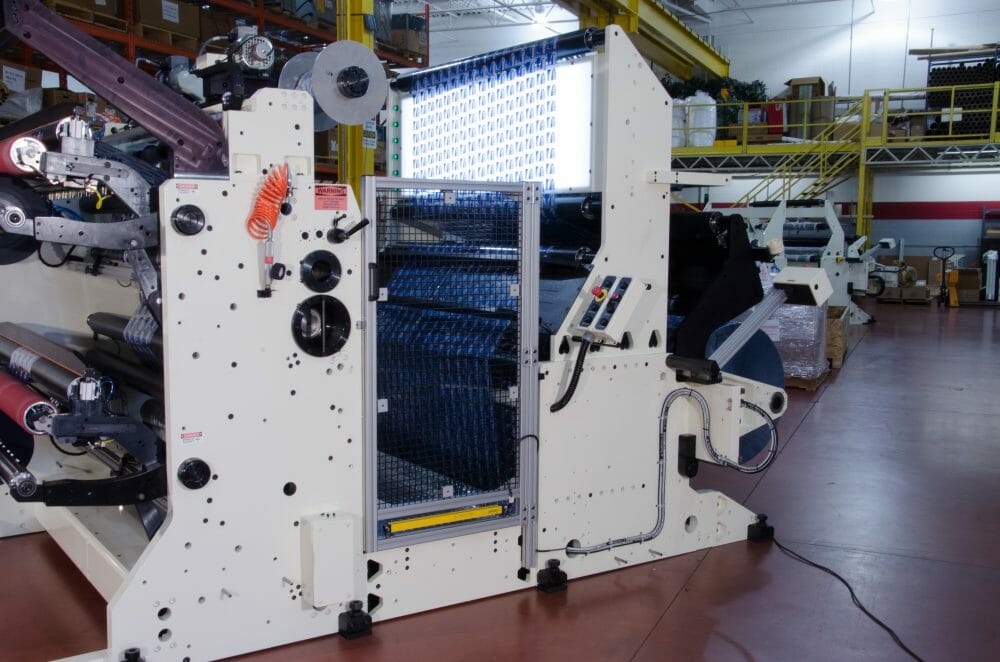
Overhead / Web Path Options
Deacro offers a variety of web path options including the standard underfeed, optional overhead (for clean room applications) or an extended inspection web path option. Extended web paths can be used to add secondary processes such as web inspection while allowing defects to be stopped at a central location for web editing before defects reach the slitting section.
Rear Position / Standard Splice Tables
To assist operators with quickly splicing in new master rolls, a rear position splice table is available. Pneumatic web clamps or combination vacuum system assist with quick and accurate splicing directly from the unwind location without needing to rethread the web to a downstream splicing location. Typically used for printed web editing, pneumatic web champs hold the web in place for the operator to perform quick and precise splices while keeping the print registration. Vacuum clamping is also available.


Safety Fencing / Scanners
Deacro offers a full range of safety features to ensure safe operation while maintaining operator access as required. Flexible designs use a combination of safety fences, gates, light curtains and programmable laser scanners to suit every application.